Gas Train Components: A Detailed Overview of Key Parts for Safe and Efficient Gas Flow
It is an essential assembly in any gas-powered system, as it ensures the safe, efficient, and reliable delivery of gas. The components of a gas train work together to manage gas pressure, flow, and safety, making it a critical part of heating, combustion, and industrial processes that rely on natural gas or other gaseous fuels.

In this article, we will discuss the key components of a gas train, their roles, and how they contribute to the overall performance and safety of a gas-powered system.
What is a Gas Train?
A gas train is a collection of components designed to safely transport and control the flow of gas from the supply line to the burner or combustion equipment. This includes regulating the pressure, filtering impurities, and ensuring that gas is delivered safely to avoid leaks, overpressure, or combustion issues. A well-designed gas train will allow for precise control over gas flow and will include various safety features to mitigate risks associated with the use of combustible gas.
Gas trains are used in a wide variety of industries, from residential gas appliances (such as water heaters and stoves) to large-scale industrial equipment, including boilers, furnaces, and gas turbines.
Key Components of a Gas Train
The components of a gas train vary based on the system's complexity and size, but typically include the following essential elements. Each of these parts serves a specific function to ensure the gas is delivered to the burner under optimal conditions:
1. Gas Shut-Off Valve
The gas shut-off valve is one of the most important components in a gas train. It is designed to manually or automatically control the flow of gas into the gas train. This valve allows the operator to completely stop the gas supply for maintenance, repairs, or safety shutdowns. In emergency situations, the shut-off valve can be quickly closed to stop the flow of gas and prevent hazards such as gas leaks, explosions, or fires.
There are two types of shut-off valves: manual shut-off valves, which require manual intervention to close, and automatic shut-off valves (ASVs), which can be triggered by sensors or control systems in response to certain conditions, such as flame failure, gas pressure drop, or other malfunctions.
2. Gas Regulator
A gas regulator is used to control and reduce the pressure of the incoming gas to the level required for safe operation of the burner. Most gas supply lines carry gas at a higher pressure than what is needed by the burner, so the regulator steps down the pressure to a safe, usable level.
Regulators help maintain consistent pressure, ensuring that the burner receives a stable gas supply for optimal combustion. They also play a key role in preventing overpressure situations that could lead to leaks, system damage, or unsafe operating conditions. Regulators may be equipped with a pressure relief valve to prevent excessive pressure buildup and provide a safety mechanism in case of system failure.
3. Flow Meter
The flow meter measures the volume of gas flowing through the gas train and into the burner. Monitoring the flow rate is essential for ensuring that the correct amount of gas is delivered to the burner for efficient combustion. Flow meters typically provide real-time data on the gas consumption rate, which can be used to track burner performance and energy efficiency.
Accurate flow measurement also enables operators to identify potential issues such as low gas supply, gas leakage, or irregularities in the gas pressure. Flow meters come in various types, including mechanical, digital, and ultrasonic, depending on the complexity of the system and the level of monitoring required.
4. Gas Filter
A gas filter is used to remove any debris, dirt, or contaminants present in the gas before it enters the burner. Dust, rust, or other particles in the gas supply can accumulate in the burner and other gas system components, reducing efficiency and causing operational problems. The filter ensures that only clean gas is delivered to the burner, preventing clogs, blockages, and damage to the equipment.
Filters typically consist of a mesh or porous material that captures particles as the gas flows through. Some filters are designed with replaceable elements, while others are self-cleaning, depending on the level of contamination expected and the maintenance needs of the system.
5. Pressure Relief Valve
The pressure relief valve is an important safety feature in a gas train. It is designed to release gas if the pressure in the system exceeds safe operating levels. Overpressure situations can lead to dangerous conditions, including gas leaks, ruptures, or equipment damage. The pressure relief valve ensures that any excess pressure is safely vented, preventing harm to the system and its components.
Pressure relief valves are set to a specific pressure threshold, and once that threshold is exceeded, the valve opens to release gas and reduce pressure. The valve automatically closes once the pressure returns to normal levels, ensuring that the gas system operates within safe parameters at all times.
6. Safety Shut-Off Valve (SSOV)
The safety shut-off valve (SSOV) is a crucial safety component in the gas train that automatically stops the flow of gas if an unsafe condition is detected. These conditions may include flame loss, pilot flame failure, or changes in pressure or temperature that could pose a risk to the system.
The SSOV is typically activated by a burner management system (BMS), which continuously monitors the operation of the burner and gas train. If the system detects a malfunction or hazardous situation, the SSOV will close to prevent further gas flow, thereby protecting the burner and surrounding equipment from damage or unsafe conditions.
In many systems, the SSOV is equipped with fail-safe features to ensure that the valve closes quickly and reliably in the event of an emergency.
7. Solenoid Valves
Solenoid valves are electrically operated valves used to control the flow of gas in a gas train. They are typically integrated into automated systems that allow for remote operation and control of gas flow. These valves open or close depending on the electrical signals sent by the control system, allowing for precise and rapid regulation of gas flow to the burner.
Solenoid valves are used to automate the shut-off process and can be activated in response to various safety triggers, such as abnormal pressure, temperature, or flame loss. They are often used in combination with other safety components, such as the SSOV, to provide an added layer of protection.
8. Vent Valve
The vent valve is used to release gas from the gas train or combustion system in a controlled manner. Venting may be required during maintenance, system purging, or when there is a need to relieve pressure within the system.
Vent valves ensure that gas is released safely and in a manner that does not pose a risk of explosion, fire, or other hazards. These valves are especially important in systems where the gas is pressurized, as they help prevent overpressure conditions that could compromise the integrity of the gas train and the associated equipment.
9. Burner Control Valve
The burner control valve is responsible for regulating the amount of gas that is delivered directly to the burner. It can be controlled manually or automatically, depending on the system. This valve ensures that the burner receives the correct amount of gas for combustion, adjusting the flow in response to changes in demand or operating conditions.
In automated systems, burner control valves are integrated with burner management systems (BMS) to ensure efficient operation and to adjust gas flow based on real-time conditions such as temperature, pressure, and system performance.
10. Safety Sensors and Monitoring Devices
Safety sensors and monitoring devices are an integral part of any gas train, as they help detect hazardous conditions such as gas leaks, flame loss, or abnormal pressure levels. These sensors send signals to the control system, which can trigger safety mechanisms like the SSOV or solenoid valves to shut off the gas supply and prevent accidents.
Common safety sensors include flame sensors, temperature sensors, and pressure sensors. These sensors continuously monitor the gas train and burner operation, providing real-time feedback to the control system.
Conclusion
Gas trains are complex and crucial systems that ensure the safe and efficient delivery of gas to burners, boilers, furnaces, and other combustion equipment. The key components of a gas train work together to regulate gas flow, maintain pressure, filter impurities, and provide safety features that protect both the equipment and the surrounding environment.
What's Your Reaction?



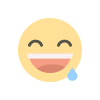


